A gantry crane can pick up and set down anywhere within a certain area. A monorail is more limited. It can work only along a line. But for many plants and factories, linear transport is exactly what they need. Julian Champkin investigates the monorail.
An item passes down a production line. Different things are done to it at each work station. It emerges at the far end as a finished product. It has travelled along a line so a monorail can carry it. And of course, the line does not have to be a straight one: bends and curves are perfectly possible. So too are switches and points, as on a railway line, so loads can be diverted along two or more different paths – or can be parked out of the way, or can overtake one another if needed. For such setups, monorails can be ideal. Electric Hoist Manufacturers

Linear coverage may seem limited. In fact a monorail can carry a load far further through a factory than any other overhead option. A wall-mounted jib crane is essentially a local solution, limited to the radius of its jib. An overhead gantry system demands a rectangular building if it is to cover it end-to-end. A monorail on the other hand can snake its way around the whole length of a factory, no matter what curving or winding route is required.
Having basically, when looked at from a distance, just one moving part – the hoist-on- a-trolley - that runs along what can basically be a bog-standard steel I-beam – though more sophisticated options are available and are usually used – the monorail is simple and therefore cheap. It is also adaptable. It bolts together, follows the curves and angles of your factory setup, and you can of course hang whatever gripping mechanism you fancy onto the lifting end of the hoist, from simple hooks to vacuum grippers to custom-fabricated lifting frames.
“Monorails are an ideal solution for predetermined and precise operations,” says Matt Baker, UK sales manager of TAWI. The company makes monorails with capacities up to 1.5t. The curves are what can make them so useful, he says: “Single tracks combined with curve segments are a combination that is often used when ventilation or other obstructions are limiting the possibility of a girder crane system,” he says. “That way, production can be followed from raw material intake all the way to final packing stations.
“Whatever the layout of your facilities, the modular nature of the system means that a solution can be tailored for your needs. Straight monorails can be combined with 45-degree angular modules to pass around obstacles, go through hallways and follow existing infrastructure with great precision. Monorail and curve modules aim to create an optimal suspension system with the highest possible integration into your operations. As an optimal solution for closed systems where the planner aims to hold high control over what is to be done, and what can be done, on the factory floor, the monorail and curve system are unrivalled.”
And also, as we said, they are low in price – but Baker adds a whole string of further efficiencies: “The monorail can be a cost-effective alternative to girder systems. It can sufficiently serve a working area along a straight line when there is no demand for sideways transportation. Having such a system when no sideways travel is needed means having nothing but the necessary. Such a minimalistic approach can be argued as the most cost-efficient, but also volumetrically-, materially-, environmentally- and spatially-efficient alternative for your operations.
“And if you’re unsure whether your operations might change in the future, the modular construction always offers the possibility of expanding, rearranging and even converting the system into an open, x-y girder crane system at any time.”
Choice of material for the rail will depend, he says, on application as well as on capacity. “For agile and truly lightweight crane systems, aluminium is primarily the material of choice.
Engineered aluminium profiles give a high strength to weight ratio for the user. The low self-weight of the lightweight crane system contributes to ergonomic manual handling for the operator. Aluminium comes in its raw, natural, appearance, which looks good, and is also the most cost-effective alternative for handling loads of up to 125 kg.
“For heavier loads, your system should be engineered from high strength, cold-rolled steel.
Stainless steel is also appropriate when the operations have high sanitary requirements such as when handling chemicals, pharmaceuticals, or food items. Steel profiles can handle up to 8 meters between the suspension points, which can be the perfect solution if the roof structure or floor area, has spatial limitations or structural constraints. The steel profiles are made from a single piece of high strength cold forming steel, which provides a strong and cost-effective product as well as resulting in a relatively lightweight crane system.
If there is no outer factor that weighs in on the preference of material, just tell us the needs of your intended operations and we will custom design a lightweight crane system of optimal performance.”
Such a solution is often a combined system where the supporting structure is of steel to carry several lifting girders made from aluminium, the girders in turn being dimensioned for the material being handled. “That creates a system that is structurally stable to hold several workstations and dimensioned for the heaviest handled load, yet easily manoeuvred by each operator,” he says.
ABUS, based 50km east of Cologne, has its HB-System for linear point-to-point transport. It claims low headroom with wide suspension spacing, and optional electric travel for the hoist trolley.
The ABUS HB light crane track system is designed as a gantry system, but being modular, it can be installed as a monorail if desired. The bridge element, normally travelling suspended on its trolleys in the crane runway tracks, is instead attached directly to the roof of the building or to suitable supports, and the trolly and hoist of course travel along it. The suspension variants are diverse, so much so that ABUS says installations are possible under conditions that “one would scarcely have thought possible.” Load capacity of the light track system can be individually selected up to 2000kg. “Limiting components to a minimum simplifies installation, saves time, and helps avoid installation faults if installing yourself,” says the company – though they also offer an installation service - and putting in a monorail rather than gantry system would certainly qualify as simplifying and minimising both installation and expense. Standard systematic ABUS plug-in connections make the electrical installation quick and safe. Modifications and upgrades are easy.
ABUS has six profile types for the running rail, all of them enclosed, and designed for different capacities and applications. “Enclosed profiles offer effective protection of the trolley, and give maintenance benefits,” says Christian Karrer, their sales manager for light cranes. “The profile cross-section with its unique design and manufacturing process also gives high quality running surfaces and greater strength, which allow large distances between suspension points even in the upper load capacity ranges by keeping the overall height low; and joints between sections are as rigid as the profiles themselves. By keeping out dust, enclosed profiles reduce the rolling friction of the trolley wheels, meaning that little force is needed when moving the trolleys by hand. Profiles are available in milled steel inside and outside galvanized, and in aluminium; the latter are lighter. ABUS uses them preferably for cranes in their gantry systems which often have to be moved by hand for specialised operating condi¬tions, such as humidity, mildly aggressive media or clean room requirements, pose no great challenge for the galvanised or anodised profiles.”
When is a monorail not a monorail? We have said that they are ideal for linear production lines; but they can also be integrated into complete systems with switches, turntables, links into underhung bridge cranes, and even swing-out ‘sling-link’ jib sections that can extend through a door into an outside space for loading or unloading components. It becomes, in effect, a network.
“In an integrated system like that, the same trolley can travel along the monorail and then onto the bridge crane, so becoming the crane trolley for a while; then back onto the same or another part of the monorail and so onward into different processing rooms or bays as required. All of that can be done without ever having to set the load down or detach it from the trolley,” says Todd Wagner, product expert, Gorbel, operating out of New York. “It means you can dispense with transfer carts or conveyors; it can all be done overhead without having any kind of stop or obstruction on the ground; your groundspace is completely clear and unobstructed.”
Gorbel can even supply drop sections (or lift sections, if you look at it the other way) that lower (or raise) a section of the rail from, say, an upper storey to a lower one, (or the other way round) to transfer and continue the manufacturing process to a ground floor space.
“Though those are not much needed, since most factories and plants spread horizontally rather that vertically,” he says. “But the basic concept of a monorail is that you can bring your load through the whole of your facility, from A to Z, with no worries about ‘where am I going to get another hoist to move the load on from here?’
Most applications, he finds, are for light lifting, low-capacity uses: “The realm we play mostly in is the 2-5t range” he says; “but you can have components and engineering to go well beyond that. Five to 10 ton is very common; you can even go to 25t if your application requires it.”
Veterinary applications are surprisingly common, both for carrying live animals for treatment and dead ones for pathology or necropsy purposes, to extract tissue to work out what they died from. An adult horse can weigh a ton, which is well within the range of a heavier-capacity monorail. More than one manufacturer mentioned this application to us. Less unexpected is in hot-metal work, pouring molten metal from ladles into moulds.
“We have a good boundary base in that area of customers within the US, and some overseas as well,” says Wagner.
Gorbel manufacture both their Cleveland Tramrail ‘Tarca’ Track patented rail and their own enclosed track systems. The Cleveland brand originated in Ohio in 1919 and after several changes of ownership was acquired by Gorbel. “We have kept the brand identity because the track is so long-lasting,” says Wagner. “Very many owners have Cleveland installations that are decades old, that still function well, that they may want to extend or upgrade, and that they think of as ‘Cleveland’.”
Cleveland patented track looks like an I-beam, but is actually very different. The secret is in the bottom flange. “It will be either three-and-a-quarter inch or four and a half inch wide – that larger size being mainly used in foundries,” says Wagner, “and it is of high-carbon hardened steel. The web and the top flange are mild steel, and they are joined to the bottom flange by an automated continuous welding machine which gives a full penetration continuous weld down the length of the beam.
“That makes it different from a conventional I-beam, where the top and bottom are exactly the same. The hardened track can take abuse for a really long time; and it has a slightly-raised running tread on it also. On a conventional beam, over time the bottom flange can bend downwards with use. The Cleveland process also gives you a consistently straight beam, with the bottom flange always precisely the same dimensions, so you don’t have to worry about working the beams on-site when you are installing to make them match up.
“And since it is an engineered product, we have been able to introduce, as a new thing this year, a rail-life calculator. You feed in the hoisting information, the loads and number of picks an hour and the number of shifts, and it will tell you how long the rail should last. You cannot do that with an I-beam, but with Tarca track it is something we can offer,” says Wagner.
Gorbel’s enclosed track system comes in aluminium or steel and is for generally lighter, more linear applications; it has fewer switching options than Cleveland track and can carry up to 4,000 lb (1.8t). “A good use for it, outside lifting, is in fall protection,” says marketing manager Scott Goforth. “If, say, a distribution facility needs engineers to go overhead over conveyor belts or the like, they can tie off to the enclosed track and still follow the whole route of the conveyor, with that safety protection should they fall.” It can also be used with the Cleveland track to make hybrid overhead gantry cranes: the strength and longevity of Cleveland track for the runways combines with the lightness of enclosed track for the bridge. Such hybrids have been available as special orders for some time; Gorbel has this year launched an online configurator for its dealer network. “It means that our dealers can now design the hybrid systems themselves,” says Goforth.
“Assembly lines and paint lines are popular places for monorails,” says Tim Bambrick, regional sales manager, Spanco. “They can of course be hung from the ceiling, leaving floor spaces completely clear, but for that the building structure does need to be reviewed by a local professional engineer. Our hangers can mount to roof trusses that are up to 14 degrees in slope. If ceilings are not strong enough we can provide custom support structures – either cantilevered columns or traditional header beams with columns.”
Spanco make enclosed track, which is, he says, is more ergonomic. “The Spanco enclosed track system takes about 1% off the force needed to start the load, and about 0.8% off the force to continue movement. Trolleys can be motorised if needed, and we have right hand switches, left hand switches, and three-way switches to change its course. Our systems can carry up to 2t on straight sections, but switches and curves are up to 1t only.”
Erikkila’s light monorail system is made in Finland using Kito hoists from Japan. They too use enclosed profiles, in steel or aluminium; “Aluminium is much used in the food industry,” says sales manager Mika Ressi. Both types have internal conductor rails to take the current to motorised trolleys. The steel profile comes in three sizes, to carry 250kg up to 2t, the aluminium in four; “But we are adding another intermediate steel profile this year,” he says. Trolleys can be motorised or manual; the wheels are steel or PVC, “or they can be rubber if the customer for any reason wants completely silent operation,” he says. A possible client for that might be the Helsinki Opera House, which has installed Erikkila monorails for scenery shifts.
“Radio control is also an option; and our trolleys have inverter control. We can customise trolley, rails or supports if required; around 50% of our customers buy standard components,50% buy something customised.” Suspension brackets can be fixed to roof I-beams, inclined trusses, or almost anything else.
“A nice feature is that the system is assembled onsite with nuts and bolts; no welding is involved. That means that if the customer moves sites, he can bring his monorail with him; and if he modifies or extends his plant, it is very simple to adapt the monorail to the changes.”
So monorails are simple, flexible and cheap. Is there anything not to like?
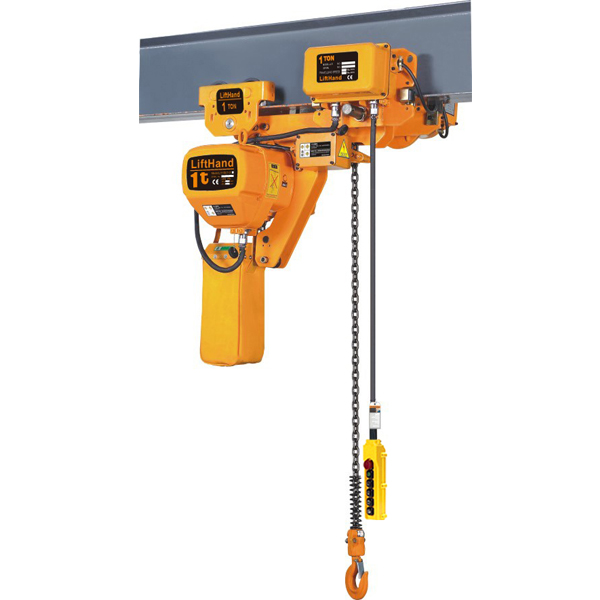
Electric Hoist Factory Progressive Media International Limited. Registered Office: 40-42 Hatton Garden, London, EC1N 8EB, UK.Copyright 2023 Progressive Media International Limited. All rights reserved.